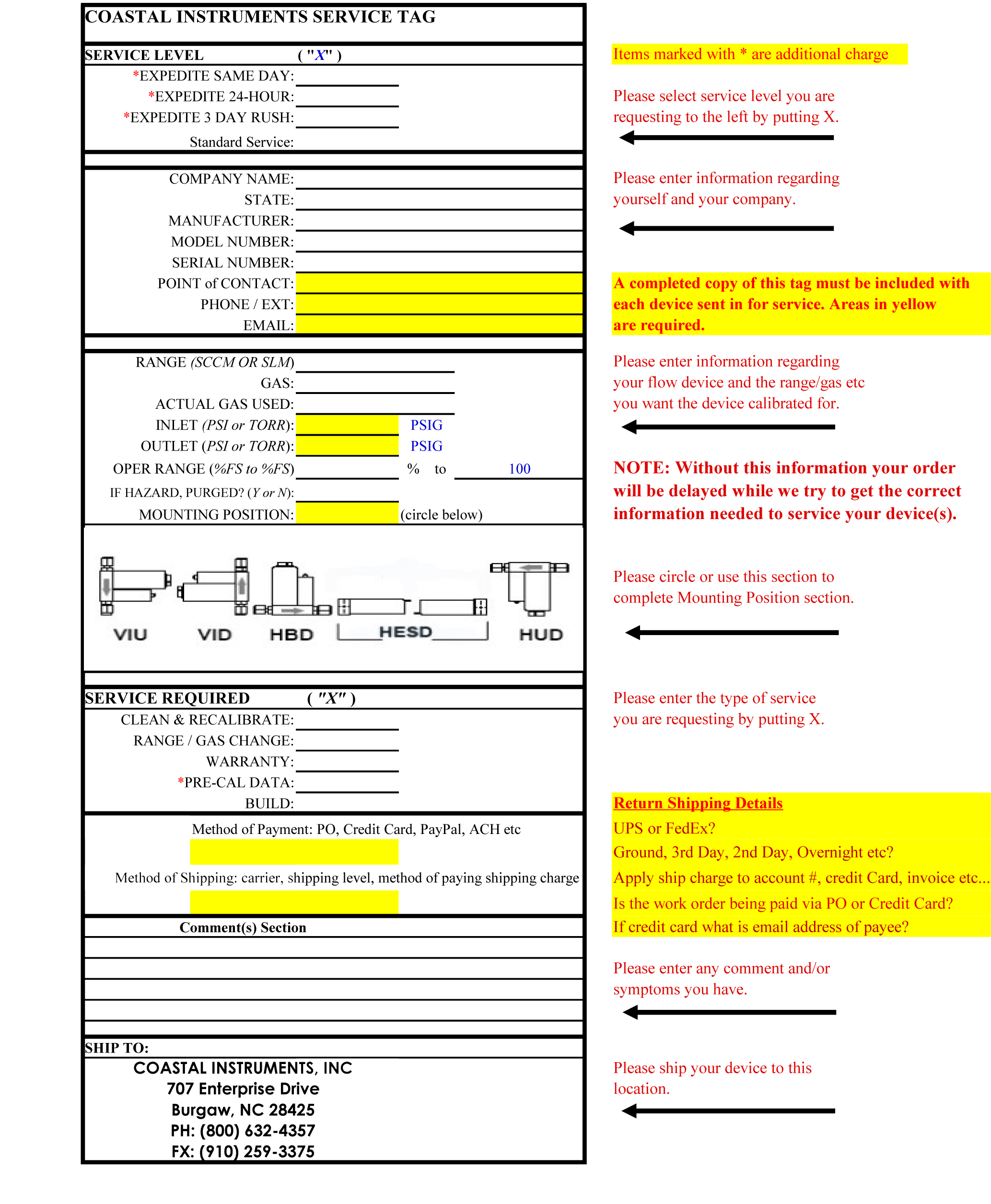
Instructions for Filling Out the Repair Tag
To ensure you get the correct service for your mass flow controller, we require specific technical information. Please complete the Repair Tags as accurately as possible. If you have any questions regarding the information required on the Repair Tag, please consult a process technician or other line personnel familiar with the device. If an accredited calibration is required, please indicate in the space for symptoms.
click on the example at right for a printable copy of the repair tag
Descriptions of Repair Tag headings:
- Service Level highlight:
- Expedite service and 3 Day Rush Service for emergency situation (additional fee)
- General service for normal 10 to 15 day turn-around.
- Other service for prior arrangements or special requests.
- Company Name, State, Manufacturer and Model No. – self explanatory
- Serial# – This is the serial number of the mass flow controller. This is a unique number which identifies the device.
- Technician – This is a very important piece of information. This is the person we can contact for information on how the mass flow controller is used or specific symptom descriptions.
- Phone # & Extension – The number and extension, as well as email address, where we can locate the Technician.
- Range – This is the flow range described on the mass flow controller, top or side decal, in SCCM (Standard Cubic Centimeters Per Minute) or SLM (Standard Liters Per Minute).
- Gas – This is the gas described on the top or side decal.
- Actual Gas Used – This is the actual gas that will be flowing through your mass flow controller in your system. This may or may not be the gas indicated on the mass flow controller decal.
- Operating Pressure: In (INLET) – This is the pressure maintained at the inlet fitting of the mass flow controller. This is usually the pressure indicated on the nearest upstream pressure gauge.
- Operating Pressure: OUT (OUTLET) – This is the pressure or vacuum maintained at the outlet fitting of the mass flow controller.
- Operating Range – This is the range of flows, expressed as a percent of full scale, you will be asking the mass flow controller to provide. If we know this information, we will provide extra attention over this range of operation.
- Mounting Position – Circle the position in which the mass flow controller will be mounted during normal operations in your system.
- Service Required – Highlight the type of service needed.
- Symptoms – These are the actual symptoms exhibited by the mass flow controller. This is very important. Try to be as exact as possible. Provide actual symptoms such as:
- The MFC output indication was zero but the system pressure was very high.
- The MFC output indication was steady at 50% but the system pressure was erratic.
- The MFC output indication drops from 35% to nearly zero every four (4) hours.
For intermittent problems, we need to know the approximate time frame needed for the symptoms to occur.
- Wrong flow range, please change to 30 sccm BCl3
If you need repair tags mailed or faxed, please call 1-800-MFC-HELP
|